The Essential Guide to Plastic Molding Tools for Metal Fabrication
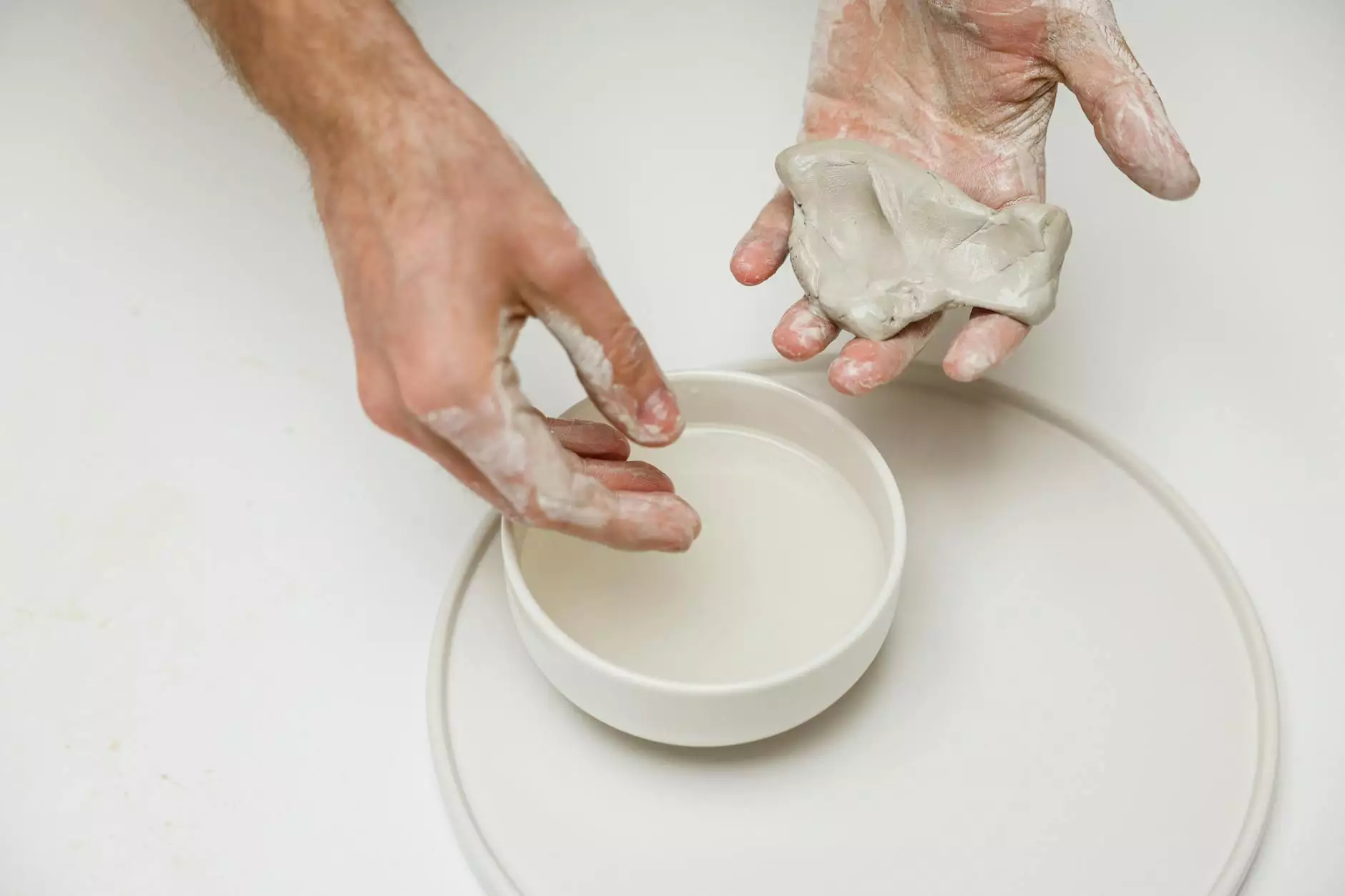
In the competitive landscape of metal fabrication, the choice of tools can dictate not only the quality of output but also the operational efficiency and profitability of the business. Among the various tools available, plastic molding tools have emerged as indispensable instruments in the production and manufacturing processes. This article delves into the significance of these tools, their applications, and how businesses like DeepMould can benefit from their effective use.
Understanding Plastic Molding Tools
Plastic molding tools refer to a range of devices and apparatus used to shape and form plastic materials through various molding processes. These tools are pivotal in the manufacturing sectors, particularly where precision and creativity are paramount. They allow for the creation of complex parts that might be impossible to produce using traditional fabrication methods.
Types of Plastic Molding Processes
- Injection Molding: This process involves injecting molten plastic into a mold to form the desired shape. It is widely used for mass production due to its efficiency.
- Blow Molding: Primarily used for producing hollow plastic parts, blow molding is used extensively for manufacturing bottles and containers.
- Rotational Molding: A method that creates large hollow items by rotating a mold while heating it, thus enabling the even distribution of plastic material.
- Thermoforming: Involves heating a plastic sheet until pliable and then forming it over a mold, often used for packaging and automotive parts.
The Role of Plastic Molding Tools in Metal Fabrication
The relationship between plastic molding and metal fabrication may not be readily apparent, yet they complement each other in many ways. As industries evolve, the use of plastic molding tools is becoming more integrated into the metal fabrication processes, particularly in the production of prototypes and component parts that suit metal applications.
Benefits of Integrating Plastic Molding Tools in Metal Fabrication
Incorporating plastic molding tools into metal fabrication can yield several advantages:
- Cost Efficiency: Tools designed for plastic molding usually have lower material costs and can significantly reduce production expenses.
- Rapid Prototyping: The ability to quickly produce plastic components allows metal fabricators to consider and test designs without the long lead times associated with conventional metal tools.
- Design Versatility: Plastic molding permits the creation of intricate designs that can enhance metal parts, improving both functionality and aesthetic appeal.
- Weight Reduction: Using plastic components in conjunction with metal can lead to lighter products without sacrificing strength.
Choosing the Right Plastic Molding Tools
Selecting the appropriate plastic molding tools is crucial for maximizing productivity and maintaining quality. Here are key considerations when choosing these tools:
Material Compatibility
The type of plastic you intend to work with is a critical factor. Different plastics have varying melting points, viscosities, and shrinkage rates. Choosing tools that align with these characteristics ensures optimal performance. Common materials include:
- Polyethylene (PE)
- Polypropylene (PP)
- Polyvinyl Chloride (PVC)
- Polycarbonate (PC)
Molding Technology
Understanding the capabilities and limitations of different molding technologies is essential. For instance, injection molding is ideal for high-volume production, while thermoforming might be better suited for low-volume projects that require rapid changes in design.
Tool Material and Durability
The material used in manufacturing the plastic molding tools will impact both the longevity of the tools and the quality of the finished product. High-quality steel or alloy materials tend to provide better results, especially for precision components.
Investment in Plastic Molding Tools: A Long-Term Strategy
Investing in high-quality plastic molding tools is a strategic decision that can lead to enhanced productivity, decreased downtime, and overall improved profitability. Businesses should view this as a long-term investment rather than a short-term expense. By enhancing your production capabilities, you set your business up for sustained growth and success.
Monitoring Performance and Ongoing Maintenance
Once you invest in plastic molding tools, continuous monitoring of their performance is imperative. Implement regular maintenance schedules to ensure the tools function optimally. This can prevent costly repairs and maintain production quality.
Case Studies and Success Stories
Companies that have embraced plastic molding tools alongside metal fabrication have seen substantial improvements in their operations. For example:
Company A: Innovative Prototyping
A well-known automotive manufacturer integrated plastic molding tools into their prototyping process. This move allowed them to quickly test and modify designs, significantly reducing the time from concept to market. The result was not only a faster production cycle but also increased adaptability to market demands.
Company B: Cost Reduction Through Multi-material Parts
A leading electronics firm shifted towards using plastic in conjunction with their metal parts. This integration resulted in the reduction of overall product weight and material costs while maintaining the product’s integrity and functionality.
Future Trends in Plastic Molding Tools
The future of plastic molding tools in metal fabrication looks promising. Several trends are shaping the industry:
3D Printing Integration
The rise of 3D printing technology is influencing how plastic molds are designed and produced. This can lead to customized solutions that cater specifically to unique fabrication requirements.
Sustainable Practices
With growing environmental concerns, the demand for sustainable materials and practices is increasing. Manufacturing companies that adopt eco-friendly plastics and energy-efficient plastic molding tools will likely see customer preference shift towards their products.
Conclusion
In conclusion, the integration of plastic molding tools in metal fabrication signifies a transformative strategy that offers multiple benefits, from enhancing productivity to fostering innovation. Companies like DeepMould serve as a pivotal resource for businesses aiming to navigate this landscape skillfully. As industries push for greater efficiency and adaptability, recognizing the value of these tools will be crucial in staying ahead in the competitive market. Embrace the future with the right tools and strategies, and watch your business thrive.