Understanding the Low Pressure Casting Process: A Detailed Overview
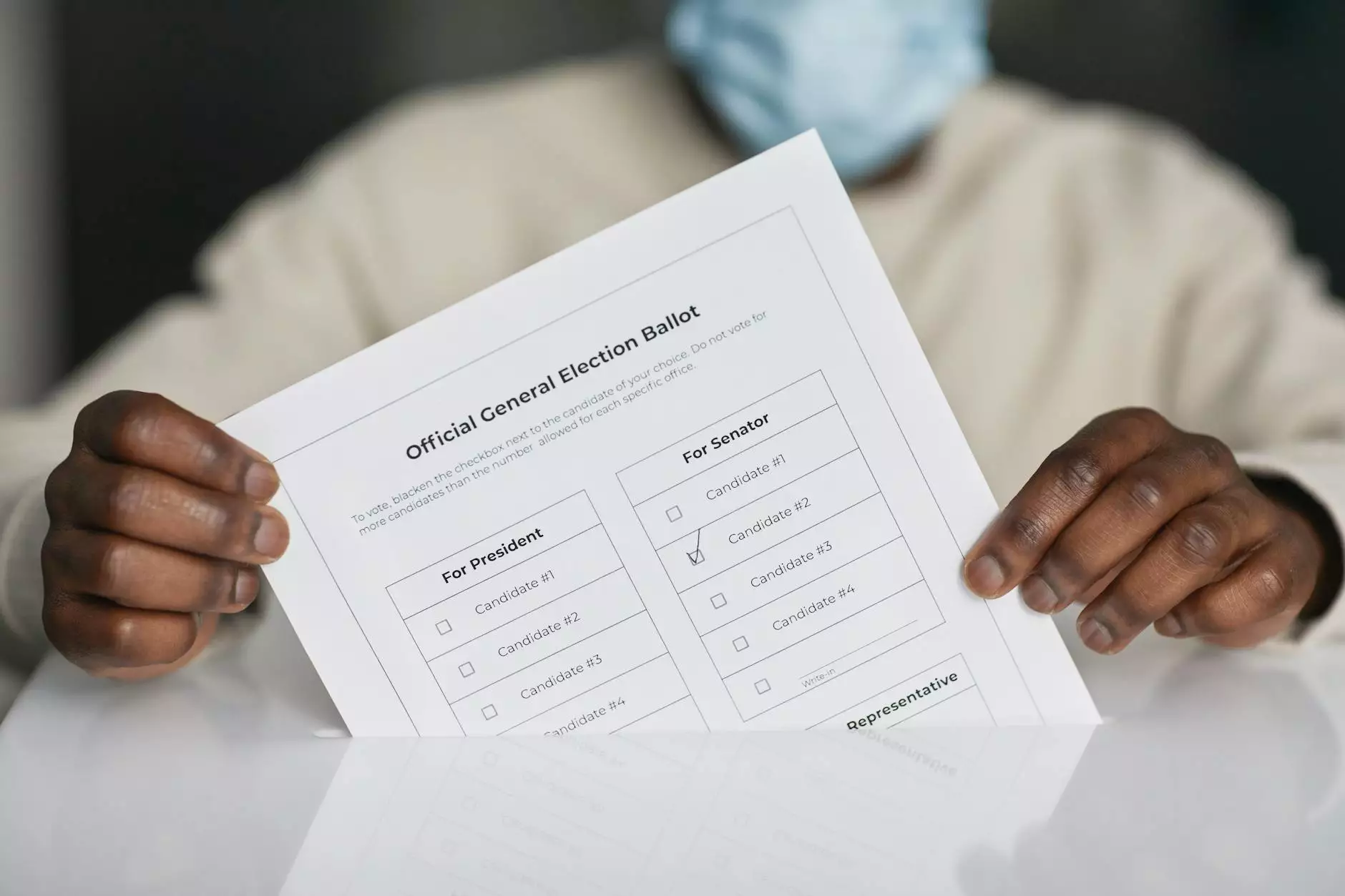
The low pressure casting process is a revolutionary technique widely adopted in various industries for its efficiency and precision. This article delves deep into the low pressure casting process, exploring its benefits, applications, and relevance in fields like art supplies, product design, and 3D printing.
What is the Low Pressure Casting Process?
The low pressure casting process, also known as low-pressure die casting, involves the injection of molten metal into a mold under a controlled low pressure. This method aims for accurate reproductions of the intended shape while minimizing defects commonly associated with other casting methods.
How Does it Work?
The process consists of several key steps:
- Melting the Metal: The metal—typically aluminum or magnesium—is melted in a furnace.
- Injecting the Molten Metal: Once melted, the metal is injected into a mold using a pneumatic device, applying a low pressure that can range from 1 to 3 bars.
- Cooling and Solidifying: The molten metal fills the mold and begins to cool, solidifying into the desired shape.
- Removing the Cast: After sufficient cooling, the mold is opened, and the cast is removed for finishing processes.
Why Choose Low Pressure Casting?
The low pressure casting process offers numerous advantages compared to traditional casting methods, making it an attractive option for manufacturers and designers.
1. Enhanced Quality of Castings
One of the primary benefits of low pressure casting is the superior quality of the castings produced. The controlled environment allows for less porosity and fewer defects, resulting in a smoother surface finish and better dimensional accuracy.
2. Cost-Effective for High-Volume Production
While there's an initial investment in mold design and manufacturing, the low pressure casting process is exceptionally cost-effective for large production runs. The speed of the process allows for high output rates, subsequently lowering the cost per unit.
3. Environmentally Friendly
This method generates less waste than traditional die casting and utilizes less energy, making it a more sustainable choice for manufacturers who prioritize green practices.
Applications of Low Pressure Casting
The versatility of the low pressure casting process lends itself to various applications across different industries:
1. Art Supplies
The art community benefits greatly from the low pressure casting process, particularly in creating unique and detailed sculptures and prototype pieces. Artists can produce intricate designs with high fidelity, enhancing the creative possibilities.
2. Product Design
In product design, the process is invaluable for creating prototypes and small batch production items. Designers can rapidly iterate their designs, testing function and aesthetics without incurring prohibitive costs.
3. 3D Printing Integration
As 3D printing technology advances, integrating low pressure casting techniques allows for the production of precise metal components from 3D printed patterns. This synergy not only enhances speed but also broadens the scope of what designers can achieve.
Technical Aspects of Low Pressure Casting
Understanding the technical nuances of the low pressure casting process can provide insights into how to optimize this method for specific projects.
1. Mold Design
Mold design is critical in the low pressure casting process. A well-designed mold not only dictates the quality of the cast but also impacts the filling pattern, cooling rate, and overall cycle time. Engineers need to account for:
- Design complexity
- Draft angles for easy removal
- Gate location and size
2. Material Selection
Choosing the right materials for low pressure casting is essential. Common choices include:
- Aluminum: Lightweight and offering excellent corrosion resistance.
- Magnesium: Even lighter than aluminum, perfect for applications where weight reduction is critical.
- Alloy Variants: Various alloy compositions can affect performance characteristics and casting behavior.
3. Parameter Optimization
Optimizing parameters like pouring temperature, pressure, and cooling rate can significantly influence the quality of the final products. Each material may require different settings, so thorough testing and validation are often necessary.
Challenges in Low Pressure Casting
While the low pressure casting process boasts many benefits, it is not without challenges. Some obstacles designers and manufacturers may face include:
1. Initial Setup Costs
High-quality molds can come with substantial upfront costs. Companies must weigh these costs against potential long-term savings in production.
2. Limited Material Choices
Although advancements are being made, the material choices for low pressure casting are still more limited compared to other methods like sand casting or traditional die casting.
3. Expertise Required
Operating a low pressure casting system effectively requires skilled professionals who understand metalworking and casting principles. Training may be necessary to ensure optimal outcomes.
Future Trends in Low Pressure Casting
The future of the low pressure casting process appears promising, with ongoing advancements enhancing its capabilities and applications.
1. Automation
Incorporating automation into the casting process can improve consistency and production rates while reducing labor costs. Automated setups can also minimize human error, creating a more reliable manufacturing environment.
2. Advanced Materials
Research in new alloy compositions and materials may open up further applications for low pressure casting, allowing industries to leverage high-performance materials in their products.
3. Integration with Digital Technologies
The integration of Industry 4.0 technologies, such as IoT and AI, into the casting process can lead to smarter and more efficient operations, monitoring parameters in real-time to optimize quality and reduce waste.
Conclusion
The low pressure casting process stands out as a highly effective method for producing high-quality metal components across various industries. Its benefits in art supplies, product design, and 3D printing make it a favored choice for many applications. By understanding the intricacies of this method, manufacturers and designers can take full advantage of its capabilities, pushing the boundaries of what is possible in metal casting.
As we move towards an increasingly technological future, the low pressure casting process is poised for growth and innovation, making it an essential aspect of modern manufacturing practices.
Explore More at Arti90
For insights on how the low pressure casting process can revolutionize your projects, and explore the full range of art supplies, product design, and 3D printing available at arti90.com. Join us at the forefront of engineering innovation!