Understanding Downhole Filters: Essential Tools for Efficient Drilling
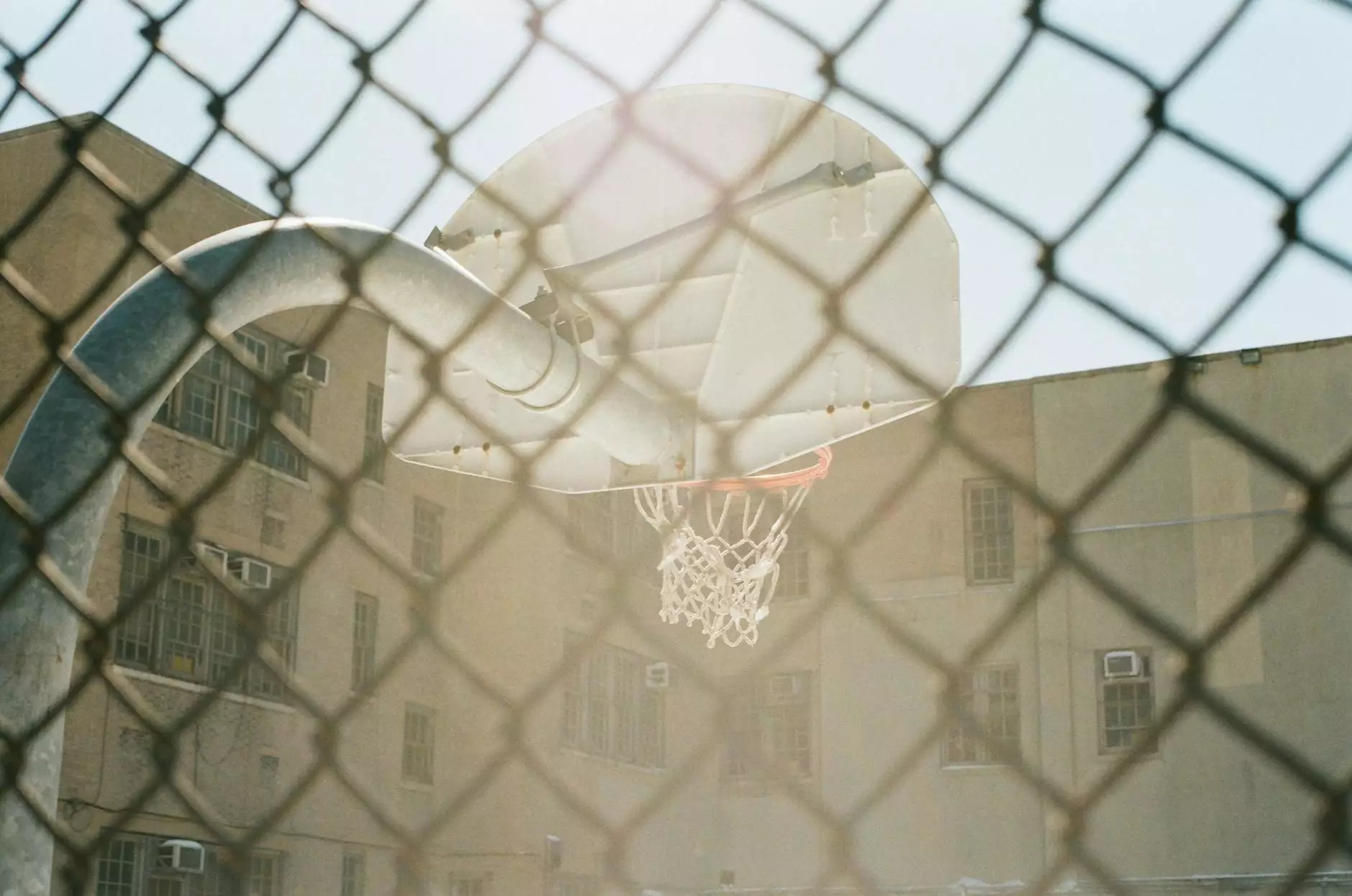
The drilling industry has seen significant innovations in technologies and equipment, making operations more efficient, reliable, and cost-effective. One such innovation is the use of downhole filters, components that have become vital for optimizing drilling operations. In this article, we will delve deep into what downhole filters are, their importance in the drilling process, and how they contribute to the overall efficiency of business operations in the industry.
What are Downhole Filters?
Downhole filters are specialized devices installed in the drilling string or within the well’s casing to prevent unwanted debris and particulates from entering the drill bit and the pump systems. These filters are crucial as they help maintain the integrity of the drilling fluids, enhance the efficiency of the drilling process, and prolong the operational life of drilling equipment.
Key Functions of Downhole Filters
The primary functions of downhole filters include:
- Debris Removal: Downhole filters efficiently capture and retain cutting debris and solid particles that arise during drilling operations.
- Fluid Quality Maintenance: They help maintain the quality of the drilling fluids, ensuring that no contaminants compromise the drilling process.
- Protection of Equipment: By preventing debris from entering sensitive equipment, downhole filters prolong the life and reliability of drilling machinery.
- Optimization of Flow Rate: Filters can be designed to optimize the flow rate of drilling fluids, improving the speed and efficiency of drilling operations.
The Importance of Downhole Filters in Drilling Operations
The integration of downhole filters into drilling operations can significantly impact both performance and cost. Here are some key reasons why they should be considered indispensable in the industry:
1. Cost Reduction
Downhole filters can lead to substantial cost savings. By filtering out debris and preventing blockages, these devices minimize the risk of costly repairs and downtime that could arise from equipment failures. With reliable filter systems in place, businesses can reduce maintenance costs and avoid the financial burden associated with unexpected equipment breakdowns.
2. Enhanced Drilling Efficiency
With the removal of debris and other contaminants, the efficiency of drilling operations improves significantly. When drilling fluids remain uncontaminated, the system can function more smoothly, reducing the wear on machinery and allowing for faster penetration rates. This efficiency not only speeds up project timelines but also enhances the productivity of drilling crews.
3. Improved Safety
The presence of debris in drilling systems can pose safety risks, leading to accidents or equipment malfunctions. By employing downhole filters, businesses can ensure a safer working environment. The filters contribute to system stability, reducing the likelihood of sudden failures that could have hazardous consequences.
Types of Downhole Filters
Understanding the different types of downhole filters available can help businesses select the right ones for their specific applications. Some common types include:
- Mesh Filters: This type uses a fine mesh to trap particulates while allowing fluids to flow through. They are suitable for various applications, including water well drilling.
- Screen Filters: These filters typically have a more rigid structure and are effective at capturing larger debris. They are extensively used in oil and gas drilling.
- Cartridge Filters: These are designed for easy replacement and offer high efficiency in filtering out contaminants.
- Hydrocyclone Filters: Utilizing centrifugal force, these filters separate water from solids and are ideal for high flow-rate applications.
Selecting the Right Downhole Filter for Your Needs
Choosing the right downhole filter is crucial for optimizing the efficiency of drilling operations. Here are some factors to consider:
1. Particle Size
It's important to assess the typical size of the debris encountered during drilling. Different filters are designed to capture different particle sizes. A thorough understanding of the geological conditions will aid in selecting the appropriate filter mesh or screen size.
2. Flow Rate
The expected flow rate of the drilling fluid should influence your choice. Filters should be capable of handling the necessary flow rate without causing significant pressure drops.
3. Compatibility with Drilling Fluids
Ensure that the filter materials are compatible with the drilling fluids used, especially in high-temperature or chemically aggressive environments. This compatibility is crucial to prevent chemical degradation of the filters.
Maintenance of Downhole Filters
To maintain the effectiveness of downhole filters, regular inspection and maintenance are essential. Here are some maintenance best practices:
- Regular Inspections: Schedule regular inspections of the filters to identify signs of wear or clogging.
- Timely Replacement: Replace filters that show signs of damage or significant clogging to ensure optimal performance.
- Cleaning Operations: When possible, cleaning the filters can help restore their functionality and extend their service life.
Future Trends in Downhole Filter Technology
As the drilling industry continues to evolve, so do the technologies associated with it. Here are some trends we can expect to see in downhole filter technology:
1. Advanced Materials
With the advent of new materials, future downhole filters may offer enhanced durability and efficiency. Innovations such as composite materials may provide superior resistance to wear and corrosion.
2. Smart Filter Systems
Integration of IoT (Internet of Things) technology into downhole filters could provide real-time monitoring capabilities. Smart filters could send alerts regarding their condition, allowing for proactive maintenance and minimized downtime.
3. Customization and Modular Design
As drilling operations become more specialized, the demand for customized and modular filter solutions is likely to increase. These systems can be designed specifically for unique geological conditions and requirements.
Conclusion
In conclusion, downhole filters are a critical component in the modern drilling industry, providing numerous benefits that include cost reduction, enhanced efficiency, and improved safety. As technology advances, the evolution of downhole filters will continue to play a vital role in optimizing drilling operations across various sectors. For businesses in the drilling industry, investing in high-quality downhole filters is not just an operational decision; it’s a strategic imperative that could significantly elevate their competitive edge in the market.
For more information on downhole filters and other essential drilling equipment, visit maverick-drilling.com and find the solutions that will propel your business forward.